Equipment being installed on rooftops has been a practice since the beginning of buildings. Before specialized non-penetrating rooftop supports were common, wood blocks were used. Contractors would typically acquire some pressure treated 4×4’s, cut, and install them under the pipes and equipment on the roof. This practice was common and accepted as the standard and in many cases wood block was specified (see below). For years it was accepted that these supports would need to be replaced over time due to rot, degradation, and deterioration. As this industry evolved it was clear that the impending failure of wood block increased risk of pipe and roof failure. This increased the dangers associated with gas leaks and potential costly damage associated with water leaks into the roof. The below specification illustrates that the fix to these inherent issues with wood was to take measures to protect the wood, but it ignores the root issue that wood will inevitably deteriorate over time.
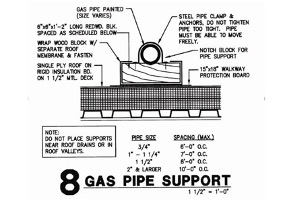
Using wood may seem easy, convenient, and cost effective but some of the less obvious drawbacks to using wood as rooftop supports are:
- Rotting over time
- Weakened properties due to being exposed to the elements.
- Under a weakened state, wood will give way to twisting and gravity loading. Making it unable to distribute load to the roof membrane properly.
- As wood degrades over time it will blow away with wind and water.
- It is costly. Including the cost of material, labor, and future damage to equipment it is supporting, along with replacement every couple years it become one of the most expensive and labor intensive support options available.
- It is not pre-engineered to distribute proper loading and often proper PSI to the roof membrane is overlooked putting the integrity of the roof at risk for future failure.
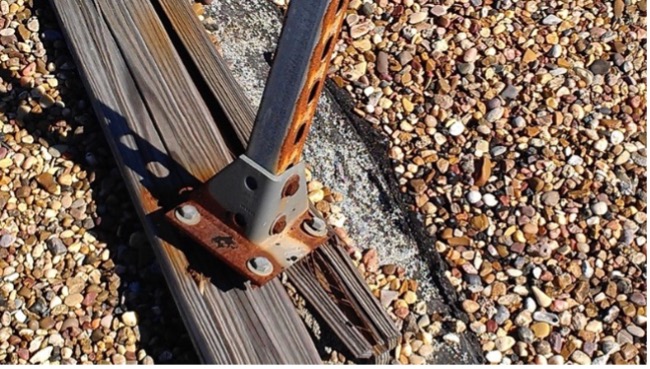
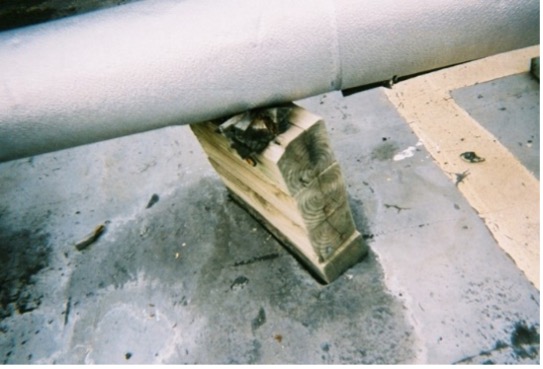
Over time the industry tried to take measures that would make wood last longer but eventually the industry learned from its past mistakes and moved away from using wood altogether. Wood has even been banned in many areas in the use of a rooftop support due to its inherent properties that will degrade over time. Now there are advanced support options that are manufactured with the use of various materials that do not degrade over time. With the advancement of these materials, the pre-engineered supports have also been designed to make installation easy, convenient, and durable to hold up to the elements for several decades. Individuals working in the industry also expect these products to lower the overall costs of the project by providing adjustable, durable, and reliable support systems. Today there is more knowledge about roofing system and equipment systems. With that understanding one can make a more informed decision about the right product to put on top of a roof membrane while allowing the equipment system to function properly for many years. These types of solutions are typically not accomplished using wood block.
As the industry continued to evolve and companies started to specialize in pre-engineered non-penetrating supports, experts in the industry emerged and recognized some of the draw backs of traditional field fabricated supports. Contractors typically welded angle iron to fit job specific conditions in the field. While the material is heavy duty and durable, it does not address load distribution to the roof, or the possibility of future adjustment. And in many cases these frames were fashioned on a wood block sleeper. As projects increase in magnitude, additional forces are applied to the overall system.
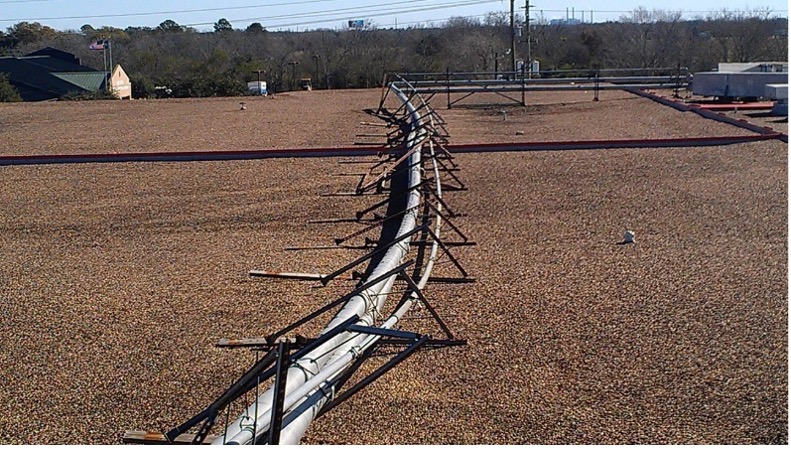
This presents the need for expert consultation regarding larger, more complex projects. Expert knowledge can help navigate seismic and wind loading forces and local building code. These loadings are being enforced more and more these days and the importance of looking at the support system rather than an individual support is imperative to a support system that will accommodate the dynamic pressures of equipment.
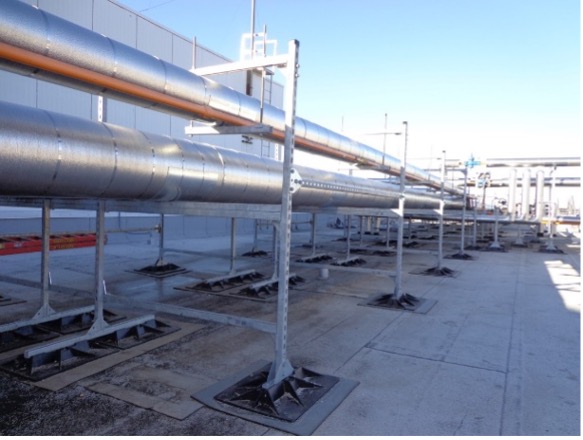